- 発行日 2025年1月7日
- 最終変更日 2025年1月7日
- 1 分
プロセス製造業におけるメンテナンス戦略
プロセス製造における補修JPを軽減するためには、明確なメンテナンス戦略が重要です。全員参加の生産maintenance(TPM)や信頼性重視のメンテナンス(RCM)は、すべての設備に適した効果的なサービスをカスタマイズするための柔軟なシステムです。その実践方法について学びましょう。
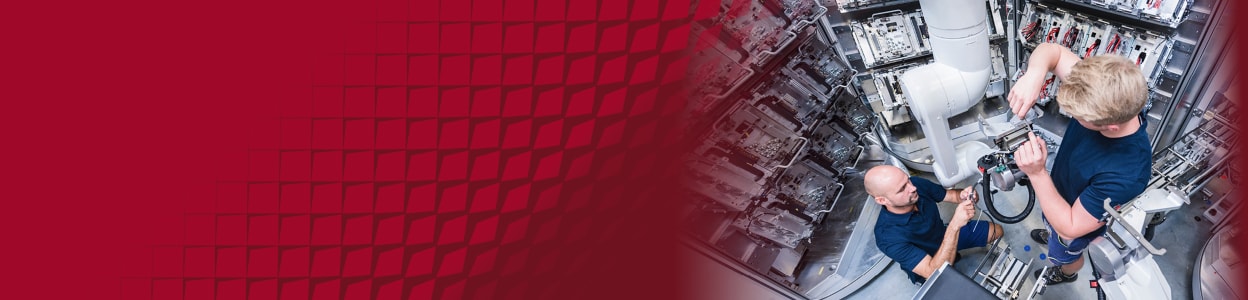
カール・ラルフ、テクニカルサポートエンジニアによるレビュー (2024年1月)
プロセス製造業におけるメンテナンスは、工場内の多様な設備を考慮すると計画が困難な場合があります。機械のニーズは、部品コスト、運転条件、交換頻度、必要なメンテナンススキルなど、様々な要因によって異なります。しかし、これらの要素を全て管理するための効果的なメンテナンス戦略が存在します。その中には、以下のような戦略があります:
- 全体設備効率(OEE)に基づく全社的生産保全(TPM)
- 特定の故障モードを防ぐことを目的とする信頼性中心保全(RCM)
これらの戦略は、施設の複雑なメンテナンスニーズに対応できる柔軟性を備えています。
メンテナンス計画の重要性
保全の重要性は言うまでもありません。故障によるコストや時間の損失を防ぎ、健康と安全を向上させ、安心感を得るために欠かせないものです。さらに、綿密で注意深い保全計画を立てることで、多くのメリットを享受できます:
- 保全を計画することで、予期せぬ交換コストに対応するのではなく、設備のサービスに必要な資金や人員を意図的に予算化できます。
- 定期的な点検をスケジュール化することで、ほとんどの問題を早期に発見し、悪化する前に対処できます。
- 設備について深く理解できるようになります。必要なもの、避けるべきこと、所有・運用にかかるコストを把握することが可能になります。また、オペレーターも設備をより適切に扱えるようになります。
- 明確な保全計画により、ドキュメントや記録が作成されます。これにより、設備故障の調査を行う際に、何が問題であったのか、そしてどのように回避すべきかを把握するための貴重なリソースを得ることができます。
さまざまなメンテナンス手法
プロセス製造では多種多様な機械や設備が使用されているため、それらのニーズに適した効率的なメンテナンス方法を確立することは容易ではありません。メンテナンスの頻度や条件に応じて、さまざまな戦略が存在します。
事後保全は、問題が発生してからそれを修正する方法です。しかし、通常、ダウンタイムやコスト、問題の診断に多大な負担がかかるため、プロセス製造では一般的に推奨されません。ただし、交換コストが低く、冗長性が確保されており、在庫も十分にある機器や部品については、事後保全の「故障まで稼働」アプローチが適用される場合があります。
予防保全では、日付や稼働時間などの固定期間を基準にメンテナンス(つまりダウンタイム)をスケジュールします。この方法は、堅牢なメンテナンスシステムとして、ほとんどの機器の問題を検知し対処することができますが、継続的なメンテナンスコストが高額になる可能性があります。
予知保全は、予防保全よりもメンテナンスコストを抑えられる戦略です。状態監視と高度なソフトウェアを活用することで、必要なときに必要なメンテナンスを確実に実施し、ダウンタイムを削減します。また、問題を初期段階で特定し、高額な修理が発生する前に対処します。予知保全には、機器、ソフトウェア、トレーニングに対する多額の初期投資が必要ですが、故障削減とコスト回避によってその投資を回収できます。
これらの概念は、より広範なメンテナンスアプローチにも応用可能で、企業全体を網羅することができます。総合的生産保全(TPM)や信頼性中心保全(RCM)は、これらのメンテナンス戦略を組み合わせ、企業のニーズに合わせたシステムを構築する手法です。
総合的生産保全(TPM)
TPMとは?
TPM(全員参加の生産保全)は、プロセス製造設備に関わるすべての関係者が、設備の設計、設置、運用、メンテナンスに取り組むことで、故障や非効率、不良品、事故を最小限に抑え、回避することを目指します。このアプローチにより、効果的なメンテナンスの取り組みがメンテナンス技術者に留まらず、企業全体に広がります。
TPMの8つの柱 TPMは、以下の8つの柱を中心に構築されています:
- 自主保全 オペレーターが日常的な保全作業を自ら行えるようにする取り組みです。機器のオペレーターは、日々の測定、記録、潤滑、清掃を通じて機械を大切に扱い、故障を回避できるよう訓練されます。また、オペレーターが問題を報告し、保全の改善を提案することを奨励します。
- 計画保全 機器が使用されていない時間帯を活用して保全作業を行います。予測保全や予防保全を活用し、機器の稼働時間と状態を監視して、サービス停止に最適なタイミングを見極めます。
- 品質維持 生産された欠陥品の数量、コスト、根本原因に焦点を当て、品質管理システムと連携します。これにより、生産性を向上させるためのメンテナンス調整が可能になります。
- 重点的な改善 異なる部門のメンバーで構成された小規模なチームを結成し、繰り返し発生する問題を調査します。その上で、設備の運用における改善点を特定し、実行します。
- 早期管理 自主保全で得た知識を活用して、新しい機械を最初から効果的に設計し、維持します。
- トレーニングおよび教育 TPMに関与するスタッフを特定し、それぞれの役割に必要なトレーニングを計画・実施します。
- 健康、安全、環境 是正措置と予防措置の両面から、健康と安全に関わるリスクを排除します。また、環境への影響を最小限に抑えることを目指します。
- 管理 材料の無駄を削減し、スケジュールや調達プロセスを改善することで、TPMの取り組みを生産部門以外の部署にも広げます。
TPMは企業文化の変革 TPMは単なる保全手法ではなく、企業文化そのものを変革する取り組みです。プロセス製造に関わるすべての人々が、設備の有効性を最大限に高めるために、自らの役割を果たすよう促します。
TPM導入ステップ
TPMを効果的に実施するための5つのステップ
- 設備の選定
TPMは、工場全体に一斉に導入する必要はありません。まずは、メンテナンスを実施しやすく、目に見えるビジネス上の利益をもたらす設備を選定することから始めます。この試行には、以下のような設備が適しています:
- 実験が容易な重要度の低いユニット
- 生産が依存する主要資産
- 頻繁に問題を起こす機械 選定した資産のメンテナンスを再構築する際は、全ての部門の協力を得ることが重要です。
- ユニットの清掃 選定した資産を徹底的に清掃し、調整してスタート時の状態に戻します。その後、5Sシステム(整理、整頓、清掃、清潔、しつけ)を活用して、その状態を維持します。この手順には、監査済みの基準を用いることが含まれます。また、日常業務の実施内容をオペレーターと合意し、必要に応じてトレーニングを実施して自主保全を導入します。
- 現在の総合設備効率(OEE)の測定
TPMの重要な原則であるOEE(総合設備効率)を測定します。OEEは以下の3つの指標に基づいて設備の性能を評価します:
- 稼働時間
- 効率
- 品質 サービスのためのシャットダウン、予定外の運転中断、不良品の発生件数を記録し、少なくとも2週間分のデータを収集します。予定外の停止の原因も詳細に記録することが重要です。
- 最悪の問題への対処 小規模なチームを結成し、選定したユニットの試運転で最も大きな停止原因に集中的に取り組みます。問題の原因と業務への影響を判断するため、証拠を収集して分析します。チームで防止策を議論し、その実施のためのスケジュールを立てます。その後、OEEを監視して対策の有効性を確認します。効果がある場合は次の問題に取り組み、効果がない場合は代替案を検討します。
- 予防保全の実施
ユニット全体を評価し、摩耗、故障、または運転ストレスの原因となる構成部品を特定します。以下のような方法で保全戦略を策定します:
-
定期点検
に基づき、一定の摩耗レベルに達した時点で交換
-
状態監視
に基づき、故障予測時間に応じて交換
-
運転時間
に基づき、定期的なメンテナンス間隔で交換 記録、監査、および設備性能の分析を通じて、この保全システムを継続的に評価・調整します。
-
信頼性中心保全(RCM)
信頼性中心保全とは?
RCMは、特定された故障を回避し、明確なパフォーマンス目標を達成することを目的としたメンテナンスシステムです。したがって、これは成功を明確に測定できるメンテナンスです。
信頼性中心のメンテナンスでは、各機械が特定の故障を防ぐために必要なケアに焦点を当てます。つまり、各機械がどのように故障する可能性があるのか、その理由や発生タイミングを慎重に分析し、費用対効果の高い方法でこれらの故障を防ぐ方法を検討します。
RCM導入ステップ
故障の原因、発生頻度を特定したら、故障が発生するたびに対処するよりもコストを抑えられるようなメンテナンス計画を立てます。
- 対象機器の特定:最も依存している機器を特定し、それがビジネスにとってどれほど重要であるか、また、その機器がダウンした場合にどのような影響があるかを評価します。以下の要因を考慮します。
- 交換費用
- バックアップが現場にあるかどうか
- 業務にどれほど支障をきたすか
- これまでに故障によってどれほどの損失を被ったか(金銭、生産ロス、ストレスなど)
- 故障を特定する:この機械はどのような理由で故障する可能性があるか?例えば:
- まったく動作しない
- 動作が不十分
- 安全上の問題を引き起こす
- 故障の原因を分析する:これらの故障のすべての原因となり得るもの、およびそれらがどの程度の頻度で起こり得るかを考えます。故障にはそれぞれ、原因となり得るものが1つ以上ある可能性があります。例えば、ドライブシャフトの回転数が低いのは、ベルトの摩耗やグリースの不足が原因である可能性があります。
- 重大性を評価する:各原因の可能性を、対応する故障の重大性と比較します。これをリスク優先度チャート(ゾーンに色分けされている)で行うと、各原因の重要性を視覚的に把握しやすくなります。
- メンテナンス計画:各機械の故障モードの原因を回避するための経済的なメンテナンス戦略を立案します。予測メンテナンスや予防メンテナンスによってこれらの原因を事前に回避すべきか、あるいは修正メンテナンスによって故障するまで稼働させることが本当に費用対効果が高く、安全であるかを検討します。これにより、貴社の資産の信頼性が確保され、真の信頼性中心保全を実現できます。
これらのメンテナンス戦略は、プロセス製造を大幅に改善することができます。RSのメンテナンスソリューションをご覧ください。設備全体の有効性を最大限に高める方法をご紹介します。