- 発行日 2024年11月28日
- 最終変更日 2024年12月2日
- 1 分
メンテナンスにおける根本原因分析
根本原因分析(RCA)により、発生原因を正確に特定し、再発を防止することができます。RCAプロセスの方法とその利点については、ガイドを参照してください。
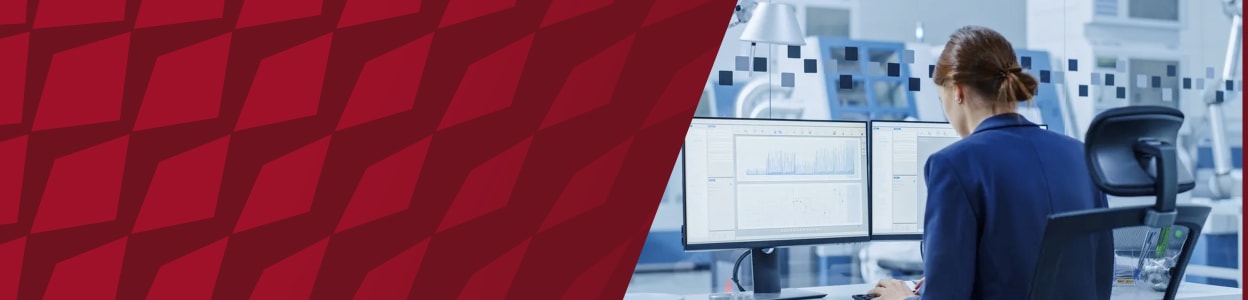
根本原因分析(RCA)は、さまざまなツールとテクニックを用いて、機械がなぜ故障したのかを理解することに役立ちます。その目的は、問題の再発を防止することです。根本原因分析のステップとその仕組みを紹介します。
根本原因分析とは?
根本原因の定義は、故障につながる大本の問題です。根本原因分析では、フィッシュボーン図、5W、パレート図などの手法を用いて、機械の故障原因を明らかにします。米国品質学会によると、根本原因とは「不適合を引き起こした要因であり、プロセス改善によって恒久的に排除されるべきもの」を意味します。根本原因とは、最終的に問題につながる因果関係を動かす最重要の原因です。
エンジニアリング分析では、根本原因分析レポートはシステム障害分析の一種となります。メンテナンスでは、技術的な問題であれ、人的要因に関連する問題であれ、システムやプロセスの結果であれ、機械的な問題の真の原因を解決することを指します。
根本原因分析の方法
根本原因分析の手法の一つは、機器の故障の「なぜ」を特定するために質問を繰り返すことです。この方法は「5W」と呼ばれています(ただし、もっと多くの(あるいはもっと少ない)質問を使用することもできます)。まず、なぜその機器が故障したのかを質問します。その答えが返ってくるたびに、根本原因が明らかになるまで、別の「なぜ」の質問が発生します。
機器メンテナンスのための他のタイプの根本原因分析には、故障モードと影響分析、フィッシュボーン図、what-if、HAZOP、フォールトツリー分析、作業安全分析、管理監督とリスクツリーが含まれます。
5W
「5W」は、故障の根本原因を特定するための最も一般的な手法のひとつです。想定されるメンテナンスのシナリオは、次のようになります:
1. 機械はなぜ故障しましたか?
答: 過熱しました。
2. なぜ機械が過熱しましたか?
答: 冷却ファンが停止しました。
3. 冷却ファンが停止したのはなぜですか?
答: 修理されていませんでした。
4. なぜ冷却ファンを修理しませんか?
答: ファンはメンテナンスの一環でありませんでした。
5. なぜファンはメンテナンスの対象外でしたか?
答: メンテナンス計画にHVAC機器が含まれていませんでしたから。
こうすることで、失敗の根本原因が特定され、再発防止のための解決策を導き出すことができます。「5W」は単純な方法であり、原因と結果の連鎖が1つである場合に最も適用できます。より複雑な問題では、RCAプロセスに他の方法が必要になります。
特性要因図(フィッシュボーン図)
フィッシュボーン図は、機械に問題が発生した場合に考えられる原因を特定するのに役立ちます。これは魚の骨格に似ており、問題の潜在的な原因を分類する視覚的な方法を提供します。魚の頭の部分には、メンテナンス関連の問題が文の形で書かれています。ページを横切る矢印は、頭(背骨)を指して描かれています。フィッシュボーン図を使用するチームは、故障の原因として考えられるものをブレーンストーミングすることから始めます。考えられる全体的な原因が特定され、バックボーンから矢印で描かれ、魚の骨が作成されます。ここで、5Wなどを使用して、各問題をさらに掘り下げ、根本原因を見つけます。根本原因が特定されると、チームは問題の再発を防ぐためにとるべき次のステップを決定できます。

根本原因分析ツール
フィッシュボーン図と5Wは、故障解析エンジニアリングに利用できる2種類のツールに過ぎません。故障モードと影響解析は、エンジニアがリスク優先順位の番号を与えることによって、メンテナンス・アクションの優先順位を決定するのに役立ちます。故障の影響を事前に予測し、軽減することを目的としており、航空宇宙や製造業で広く使用されています。
そのメリットとして、生産コストの最適化や、是正処置の優先順位をつけるための構造化されたフレームワークが挙げられます。メンテナンスだけでなく、ビジネスプロセスや製品設計・開発の改善にも利用できます。
フィッシュボーン図と同様に、フォールトツリー分析は、ブール論理を使用して、人的障害とシステム障害をマッピングする図解技法です。フォールトツリー解析は、資産の故障とサブシステムの関係を記述し、ロジックを使用して原因と影響を特定します。
パレート分析とパレート図は、イタリアの経済学者ヴィルフレド・パレートの研究に基づいています。彼は、結果の80%は原因の20%から生じると述べています(パレートの原理、または「80/20の法則」として知られています)。エンジニアはパレート図を使って、ほとんどの故障が少数の要因によって引き起こされていることを示します。そして、影響の大部分をもたらす原因を修正することに優先順位をつけることができます。
シックスシグマの方法論は、メンテナンス体制を改善し、根本原因分析を実施するための分析にも使用できます。シックスシグマはDMAICプロセス(定義、測定、分析、改善、管理)を使用し、生産環境におけるエラーを最小限に抑えます。
根本原因分析の例
上記のテクニックはすべて、エンジニアが機械の故障原因を特定する際に使用されます。故障モードと影響解析(FMEA)もまた、広く使用されています。FMEAは、機械、製品、プロセスにおけるすべてのエラーを探し出します。
最後に、コンピュータ化されたメンテナンス管理システム(CMMS)は、エンジニアが故障発生時の資産メンテナンスデータを分析することで、根本原因分析を行うこともできます。例えば、CMMSによって発行される作業指示書は、問題とその解決方法に関する情報を提供します。
根本原因分析のメリット
根本原因分析には多くのメリットがあります。それらは以下のとおりです:
効率性向上
機械の故障原因を特定することは、システム、プロセス、人的要因を改善する方法を提供します。これにより、製造作業の効率を高めることができます。
コスト削減
将来の故障を防止することは、修理やメンテナンスにかかる費用を削減することにつながります。また、計画外のダウンタイムは非常に高くつきますが、RCAはこれを防ぐのに役立ちます。
ダウンタイムの低減
機械が故障しにくくなるため、ダウンタイムが短縮されます。これにより、生産性が向上します。