- 発行日 2024年4月26日
- 最終変更日 2024年4月26日
- 1 分
コンディションモニタリング

2022年一月公開
メンテナンスの一環として状態監視を導入することで、生産性が向上し、計画外のダウンタイムが削減されます。機械の複雑化が進むにつれて、工業生産における状態監視の信頼性はますます重要になっています。状態監視は、機械やシステムを点検せずに維持管理することで、効果的な予知保全を実現し、製造工程が高いパフォーマンスを発揮し、生産工場の全体的なコストを削減できます。この記事では、状態監視の導入方法をご紹介します。
コンディションモニタリングとは?
コンディションモニタリング(状態監視)とは、工業生産における監視技術の使用を指します。これは、機械やシステムの監視を行い、エラーを早期に発見し、生産停止時間を最小限に抑えることを目的とします。センサーは振動や温度などの個々の機械パラメータを監視し、その結果を評価ユニットに報告します。つまり、機器の故障が発生する前に不具合を検出し、修正できるため、機械を迅速に停止させることが可能です。コンディション・モニタリングは、主にプロセスや製造工場で使用され、通常は長時間(継続的に)稼働する回転または可動コンポーネントを持つ機械に適用されます。
予知保全: 常に一歩先を
予知保全は古くからの概念ですが、インダストリー4.0やIIoTなどの技術の進歩により、その実践が加速しています。従来、予防保全が一般的な手法であり、定期的なメンテナンスによって機器の故障を防ぎ、機械の稼働状態を良好に保つことが求められてきました。
予知保全のコンセプトは、これらの手法をさらに進化させています。予知保全プログラムは、必要なときにのみメンテナンスを実施することを目指しています。この目標を達成するために、デジタルセンシングシステムを使用して、機械のさまざまな運転特性(振動、熱、電流など)を監視します。この状態データを活用して、摩耗や性能劣化がいつ介入を必要とするかを予測することができます。そして、これらの予測に基づいて適切なアクションを実施することで、予知保全が実施されます。
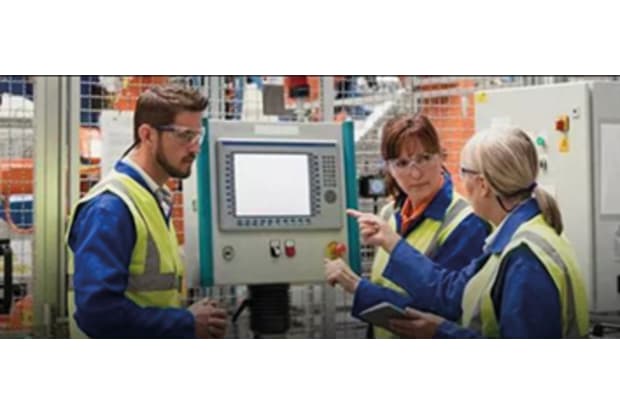
コンディション・モニタリングに必要なもの
ケーブルの敷設や水漏れの修理から大型機械の整備まで、RSの製品群には業務を円滑に進めるために必要なものが揃っています。
コンディション・モニタリングと予知保全が果たす役割とは?
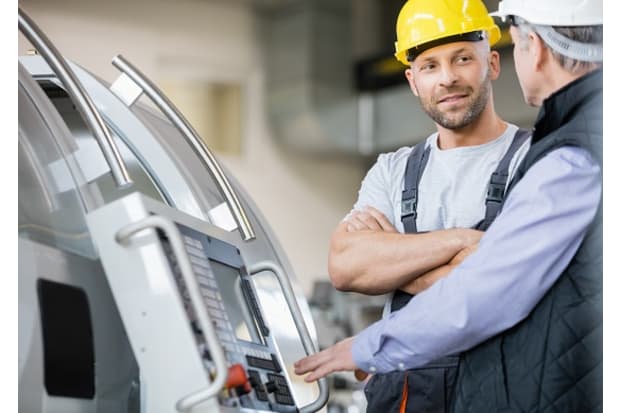
現在、多くの産業は年中無休で稼働し、フル稼働またはそれに近い状態で操業しています。このような状況下で、稼働率が上がるにつれて、機械のメンテナンス手法を効率的に改善し、ダウンタイムを削減し、生産設備をスムーズかつコスト効率の高い方法で稼働させる必要があります。そのために、コンディション・ベース・モニタリングが重要な役割を果たします。
コンディション・ベース・モニタリングは、生産設備の予知保全において重要なツールの一つです。従来の目視による保守点検を、近代的でデジタルな、そして多くの場合自律的な方法で置き換えることで、機械の最大限の活用を可能にし、保守チームへの依存を軽減します。
センサーによるモニタリング技術は、プロセスと機械データの評価に基づいて、予測的で点検不要のメンテナンスを実現します。これらのデータコレクターはリアルタイムの情報を処理し、メンテナンスの必要性を予測し、機械の故障を事前に検出することができます。これにより、予期せぬ故障による生産ダウンタイムを回避し、コスト削減を実現することが可能です。
データの収集、デジタル化、送信に加えて、特定の故障モードや事象の予測計算だけでなく、保存、分析、評価も重要な焦点となります。クラウドに接続されたソリューションは、この点で最適であり、センサーや監視ゲートウェイから分析ツールにリアルタイム・データが継続的に流れ込み、メンテナンス・チームに即座にアクションの必要性を知らせることができます。
すべての状態監視と予知保全のタスクは、最終的に企業のコスト最適化と利益最大化につながります。マッキンゼー・グローバル・インスティテュートが実施したIoTに関する調査によれば、ダウンタイムを最大50%、メンテナンスコストを最大40%削減できることが示されています。これは、最大6300億米ドルの節約に相当します。
予知保全と状態監視の利点は以下の通りです:
- メンテナンス活動の正確な事前計画
- 修理作業の削減
- 生産プラントの予期せぬ故障の回避
- 稼働時間の増加
- プラントの耐用年数を延ばす
- スペアパーツ管理の最適化
- より効率的な人員管理
- より高いプラントの安全性
- 事故の最小化
コンディション・モニタリングの仕組み
センサーは、様々な方法で資産や機械を監視し、早い段階で問題やエラーの原因を特定するために使用されます。コンディションベースメンテナンスセンサの主な特徴は以下の通りです:
- 振動分析と診断:振動センサは、回転機械の軸やベアリングの監視に使用されます。
- 作動油中の粒子の検出(油の状態分析):潤滑油の組成を電子顕微鏡でスキャンできます。これにより、機械の円滑な機能を確保し、新しい材料を迅速に注文することができます。
- 赤外線モニタリング(赤外線サーモグラフィ):特に電気ケーブルや接点では、過度の発熱は部品故障の兆候となることがあります。赤外線またはサーモグラフィ・センサを使用して、発熱の偏差を検出することができます。
- 音響モニタリング(超音波およびアコースティックエミッション):デジタル超音波装置は、ベアリングの高周波信号を測定し、音響信号として評価することができます。これにより、高速機械アプリケーションや高圧流体において特に重要な、モーションベアリングの摩擦や欠陥の予測が可能になります。
- オイル状態センサー:センサーは、重大な汚染を特定するために、組成の分光学的オイル分析を行うために使用されます。汚染粒子の種類によっては、その原因を特定し、適切な対策を講じることも可能です。
コンディション管理におけるセンサーの活用
効率的な状態監視には、センサーデータによる機械とそのさまざまな物理的コンポーネントの監視が必要です。これには、振動、圧力、温度、ホール効果センサー、赤外線カメラなどが含まれます。
その結果、数多くのアプリケーションが生まれます。以下に代表的な例を挙げます:
- フォークリフトと射出成形機:センサーは作動油の化学組成を制御します。
- 遠心分離機:センサーが回転軸の振動、速度、回転速度を監視し、狂いが生じた場合に
- 故障の可能性を報告します。
- 包装機:状態監視では、圧力センサーと流量センサーを使用して、空気消費量、作動圧力、およびサーボ空圧駆動システムの軸の機能をチェックします。
- レシプロコンプレッサー:加速度センサーと変位センサーは、クロスやシリンダーヘッドの絶対振動と、サポートリングなどの材料の摩耗を測定します。
- 冷却装置:液体または気体媒体用の温度センサーは、冷却回路の温度を制御するための測定値を提供します。
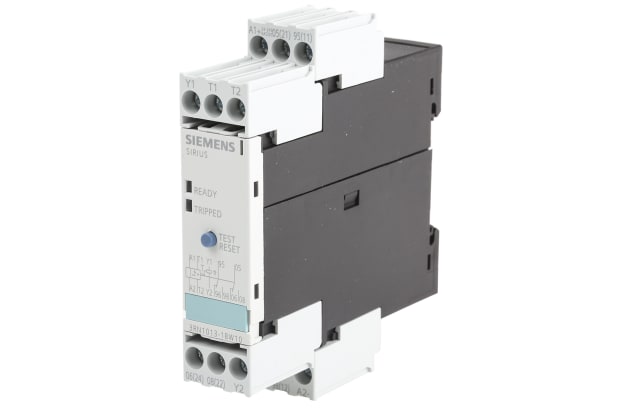
監視リレーの用途
これらのリレーは、機械の機能を監視し、障害を検出するとサーキットブレーカを起動します。 リレーの最も一般的な監視アプリケーションには以下が含まれます:
- 電圧監視
- 位相監視
- 温度監視
- 電流監視
- 周波数監視
- 速度監視
- 回転数監視
- モーター温度をカバーするサーミスタ付き特殊リレー
状態監視システムによるエンド・ツー・エンドの監視
コンディション・モニタリング・システム(CMS)は、機械のデータを評価するだけでなく、あらゆるエンド・デバイスのデータを一元的に収集、調整、検索することができます。例えば、企業は個々の機械の状態に関するデータ(メンテナンス)、生産工程全体に関する情報(工程管理)、あるいは故障原因の評価や損傷統計(品質管理)を従業員に提供することができます。機械データに加えて、建物管理を統合し、生産工程全体を体系的に最適化する目的で、生産室の温度やセキュリティドアの状態を監視することもできます。
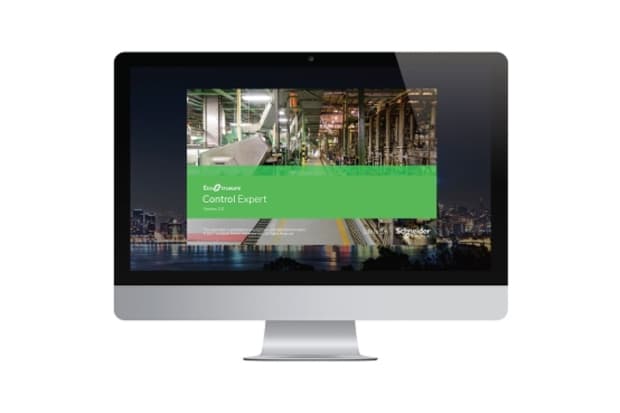
予知保全用PLCソフトウェア
優れたプログラミングソフトウェアは、機械の状態を効率的に監視し、PLC(プログラマブルロジックコントローラ)インターフェースを介して収集されたデータを評価するための基盤となります。シュナイダーエレクトリックのEcoStruxure Control™は、IoT対応のオートメーションとオープンなプラグアンドプレイアーキテクチャを組み合わせたデジタルプラットフォームです。
主な特長は以下の通りです:
- すべてのIEC 61131言語(LD、IL、ST、SFC、FBD)と構造体のサポート
- 適応可能なアプリケーションのためのマルチタスク構造
- XML、COM、DCOMによる簡単なインポート/エクスポート
- デバッグ、オンラインサービス、PLCシミュレータの提供
- PL7およびコンセプトコンバータの統合
- ライセンスフリーのライブラリ(PLCopen、Fuzzy、AGAなどのサポート)
ワイヤレスCMSシステム
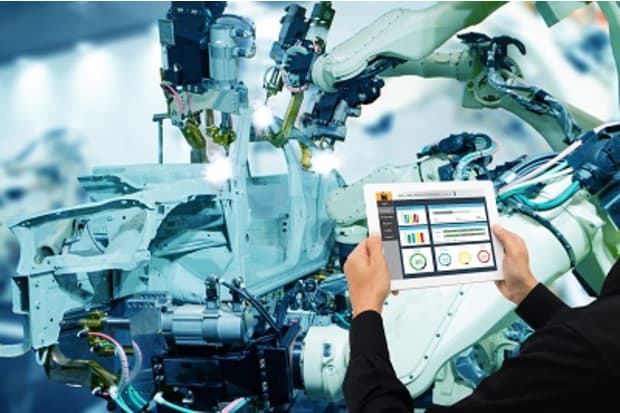
産業モノのインターネット(インダストリー4.0)によるネットワーク化の進展は、生産工場のエンド・ツー・エンドのデジタル化、モニタリング、評価(メンテナンス4.0)など、産業企業のプロセス管理に新たな可能性を生み出しています。
製品、プロセス、生産手段にはスマートセンサーが搭載され、ワイヤレスでデータが送信されます。これにより、ケーブルが損傷してもデータ評価が損なわれることはありませんし、乱雑な生産エリアに追加のケーブルを設置したり敷設したりする必要もなくなります。ワイヤレス技術を搭載したセンサーは、例えば機械に直接取り付けることができ、振動データはワイヤレスで評価ユニットに送信されます。
必要なだけ、可能な限り少なく
アップグレードを価値あるものにするために、状態監視をどの程度利用すべきかは、企業がリアルタイムのデータ取得で何をしたいかによります。機械やシステムの完全な電子制御にはコストがかかるため、理論的には、産業界の大企業にしかペイしないはずです。しかし、中小企業がコンディション・モニタリングなしでやっていく必要はありません。むしろ、競争力と未来志向を維持できるよう、自社に合ったデータ主導の枠組みの中で実施すべきです。どの機械や資産にモニタリングが必要かを評価するために、それらは異なるクラスに分けられます。目的、ダウンタイムとその影響、修理の手間、スペアパーツの入手可能性、一般的な状態と安全面に応じて、生産プロセスに対する重要性で優先順位を付け、管理強度を決定します。そして、個別に費用対効果の高いメンテナンス戦略を立案します。
- 重要部品: 生産プロセスに不可欠な機械は、常に積極的に監視する必要があります。
- 重要なコンポーネント: 非重要部品:重要ではあるが、それがなくても生産工程は稼動できる機械は、状態監視が可能です。
- 標準部品: 一般的に使用され、交換や修理が容易な機械やコンポーネントについては、定期的な手動メンテナンスで十分です。
将来的には、リモート・フロム・ソース・サービスがますます重要な役割を果たすでしょう。システムが複雑化するにつれ、トラブルシューティングの知識も増えます。特別なアプリケーションを使用すれば、メーカーは、モニタリング・システムによって検出されたエラーを直接評価し、必要であれば、リモートで自動的に解決することができます。これにより、監視の労力はさらに軽減されますが、第三者による機密データへのリモートアクセスが必要になります。不正アクセスから守るためには、さらなるITセキュリティ対策が必須となります。
個々のケースにおいて、導入が企業にとって実際に価値があるかどうかは、何よりもセキュリティ・レベルによって決まります。
総合的な設備効果とはどういったものか?
OEE(Overall Equipment Effectiveness)は、日本プラントメンテナンス協会が実施している指標であり、生産プラントの付加価値を測定するものです。ダウンタイムロス、電力ロス、品質ロスなど、最も一般的な生産性問題を考慮しています。OEEの計算、およびその監視と改善は、状態監視の一部であり、制御と密接に関連しています。OEEは、生産性、収益性、総合的な有効性など、関連するコスト面を分析し、製造プロセス全体を考慮に入れて、企業全体のレベルで比較できるようにするのに役立ちます。OEE値は、0~1または0~100%の間で設定されます。
OEEの計算式は以下の通りです: OEE=稼働率×効率×品質
具体的な計算方法は以下の通りです:
- 稼働率(Availability):稼働率=稼働時間/生産計画時間
- 効率(Performance):効率=生産量/計画生産量
- 品質(Quality):品質=欠陥のない製品/生産量