- 発行日 2024年11月28日
- 最終変更日 2025年1月10日
- 1 分
インダストリー4.0とメンテナンスの未来
デジタル技術と製造業が融合する第4次産業革命は、企業の製造方法、そしてメンテナンスの実施方法にも変革をもたらしつつあります。このガイドでは、インダストリー4.0が機械メンテナンスにどのような変化をもたらしているのか、またセンサーネットワークとビッグデータを活用したメンテナンスへの予測的アプローチの導入方法について紹介します。
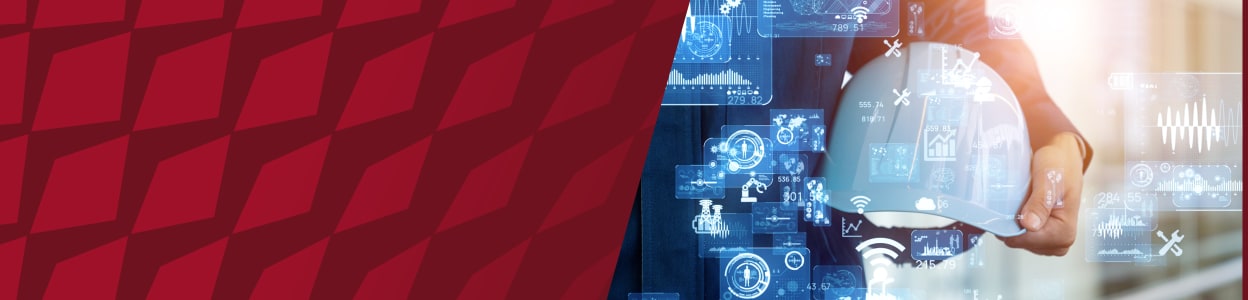
ソリューション・エンジニア、デイビッド・カーマイケルによるレビュー(2023年10月)
インダストリー4.0には、AIや機械学習から、産業用モノのインターネット(IIoT)、ロボット工学、クラウドコンピューティング、AR(拡張現実)、VR(仮想現実)に至るまで、メンテナンスに影響を及ぼすさまざまな技術が含まれています。インダストリー4.0におけるメンテナンスは、すでにこれらのイノベーションを活用しています。たとえば、センサーのネットワークとそこから生成されるビッグデータは、すでにさまざまなセクターの状態監視用途で利用されており、機械学習は機械が故障する前にメンテナンスの必要性を予測するのに役立っています。
第4次産業革命の一環として変化するメンテナンス技術の展望については、このガイドを読んでください。
メンテナンス技術
インダストリー4.0には、機械修理の方法を変えつつあるさまざまな技術があります。これらのさまざまなタイプの技術を紹介し、それらがメンテナンス戦略でどのように活用されているのかを説明します。
産業用モノのインターネット(IIoT)
産業用モノのインターネット(IIoT)とは、生産環境において機械、製品、部品をインターネットに接続することです。機器やデバイス上のセンサーやRFIDタグは、状態や位置に関する膨大な量のリアルタイムデータを提供し、メーカーがスペアパーツの在庫を管理し、機械のダウンタイムを削減します。
IIoTの実例として、状態監視と予知保全があります。これは、機械上のセンサーのネットワークによって促進され、性能を監視し、エンジニアがメンテナンスを決定するためのデータを収集・分析します。このデータにより、技術者は機械がいつ故障するかを予測し、予防保全とは異なるアプローチで早期に介入することができます。予防保全の例としては、機器メーカーが決めた定期的なスケジュールに従って機器をメンテナンスすること(定期保全)や、使用状況に応じて機器をメンテナンスすることなどがあります。
IIoTは、より広範な資産管理にも大きな影響を及ぼしています。例えば、電力や水道のネットワークなどのインフラ事業者は現在、センサーを使用してネットワーク全体のデバイスを接続し、資産の健全性(またはそうでない場合)を示すデータを収集する能力を持っています。その結果、現場にいるメンテナンスエンジニアの設備保守活動に必要な情報がもたらされます。
ビッグデータ
ビッグデータとは本質的に、さまざまなソースからのデータが増えることを意味します。多くのデータを持つことで、ビジネス上の問題をさまざまな方法で解決できる可能性が広がります。そのためには、インダストリー4.0のもうひとつの重要な要素であるクラウド・コンピューティングが可能にするリソースが必要です。従来のコンピュータリソースでは対応が困難です。
機械からの膨大なデータの収集と分析に基づいて行われる予知保全は、ビッグデータの実例です。
オートメーション
オートメーションに関して、インダストリー4.0のメンテナンスで使用される代表的な例はロボットです。メンテナンス用ロボットは、機械や設備の点検、現場の清掃、漏水の検知などに使用されます。
ロボットをメンテナンスに使用するメリットには、以下のような点が挙げられます:
- 安全確認のない、人に危険な作業を実行
- 正確に一貫した作業を長時間継続
- 風力タービンのブレードなど、困難な場所での作業
- 手作業では面倒で時間のかかる作業の代行
ロボットは何十年もの間、商品の製造に使われてきましたが、インダストリー4.0のメンテナンスにおいて、その存在感をますます高めています。
デジタルツイン
デジタルツインとは、物理システムの高度なシミュレーションです。エンジニアは、実際の物体や設備に関するデータを収集し、そのデータをデジタルモデルに入力します。その後、モデルを変更・更新することで、対象物やシステム(例えば、自動車、工場、航空機など)の改善点を特定し、その物理システムに変更を加えて改善することができます。
このアプローチの特長には、製品開発や設計プロセスを支援するために、新しいシステムの反復シミュレーションを高速に行うことができるため、改善スピードが速いことが挙げられます。インダストリー4.0のメンテナンスに関しては、デジタルツインはシステムの機能性に関する洞察を提供します。また、エンジニアは、物理的な環境で時間と費用をかけることなく、変更をシミュレートし、メンテナンスの結果を確認することができます。
予知保全
予知保全は、IIoTの機能を活用し、故障を事前に察知するものです。このメンテナンスシステムは、センサー技術とコンピュータ能力の進歩に後押しされ、近年急速に普及しています。
定期的なメンテナンスとは異なり、予知保全システムは機械性能の異常を特定し、有害な故障が発生する前にエンジニアが修理を行うことを可能にします。これにより、メンテナンスの頻度を最小限に抑え、予定外のダウンタイムを回避し、コストを削減することができます。
通常、予知保全では、機械にセンサーを設置します。これらのセンサーは、機械の性能の異常を明らかにする振動、熱や超音波情報を検出します。これらの異常は、エンジニアに故障の発生を示し、故障が悪化する前に介入することを可能にします。
予知保全は、非常に大量のデータ(ビッグデータ)の収集と、それを迅速に分析して保全の意思決定を行う能力に頼ります。例えば、振動分析によって明らかになる典型的な問題には、ベアリングの不具合や部品の緩みなどがあります。その他にも超音波技術によって、圧縮空気システムの漏れを発見することができます。
その他の予知保全技術には、赤外線サーモグラフィとモーター回路解析があります。赤外線サーモグラフィは、機械や部品から放射される赤外線をカメラで測定します。放射量が多いほど温度が高くなります。赤外線サーモグラフィは資産が過熱していることを示し、モーターの電気的・機械的欠陥のチェックに使用できます。
一方、モーター回路解析は、電気的不均衡や絶縁劣化を明らかにすることで、モーターの健全性を評価します。
予知保全のアプローチは、機械が故障したときに修理することに頼る事後保全とは全く逆のアプローチであり、予定された活動ではなく継続的な活動であるため、予防保全の例とは異なります。
インダストリー4.0のメンテナンスにおけるメリット
インダストリー4.0技術のおかげで、メンテナンスエンジニアにとっては大きなメリットがあります。それは以下の通りです:
高い効率性
対象となるメンテナンスは、メンテナンス活動を最適化し、不必要な処置の必要性を減らすはずです。そのため、従来の定期メンテナンスよりも効率的であり、機械の故障を待つよりもはるかに効率的となっています。
コスト削減
予知保全のアプローチを用いて機械のダウンタイムを削減すれば、工場の生産性が向上するため、コスト削減につながります。また、技術者の時間を最大限に活用することで、コストも削減できます。そして、資産が長持ちする可能性があるため、機械への投資収益率が向上します。
信頼性の向上
予知保全は、問題になる前に問題を特定し、機器の故障リスクを低減します。つまり、機械の信頼性を高めることができます。
インダストリー4.0技術をメンテナンス対策に統合する方法
予知保全は、インダストリー4.0技術を初めて機器のメンテナンスに使い始めるメーカーにとって、重要な分野とみられます。メンテナンス対策は、データの収集方法を検討することから始めます。
メーカーは、IIoTを使用してメンテナンスの生産性と効率を向上させる方法を検討する必要があります。最初のステップは、機械からデータを収集することです。予知保全を実施する計画であれば、データを収集する重要な資産、つまりビジネスに不可欠で、故障したときに最も大きな問題を引き起こす資産を特定することが重要です。各機械について、計画外のダウンタイムを減らすことと、投資に対する潜在的な収益の観点から、何を目指すのかを検討します。
また、メンテナンスを実施するために介入するかどうかを定義するパラメー タについても検討する必要があります。機械が確立されたしきい値を超えた場合、メンテナンスを実施する必要があることを示します。例えば、超音波センサーを使用し、機械が特定のレベルに達したら、メンテナンスが必要であると判断することができます。これは、定期的なメンテナンスが計画的に実施される予防的メンテナンスとは異なります。
また、状態監視用のセンサーを選び、設置する必要があります。振動解析センサーや赤外線カメラなどが考えられます。IIoTデバイスをコンピュータ化されたメンテナンス管理システムにリンクさせることを検討することで、機械をリアルタイムで監視し、膨大な量のデータを収集、分析、保存することが可能になります。
組織がこのような最先端の新技術を取り入れる際には、従業員のモチベーションを維持することが重要です。メンテナンス技術者やエンジニアがインダストリー4.0を理解していなければ、最新技術を導入した企業もうまくいきません。
そのため、どの資産を対象とするか、どこでどのようにデータを収集するか、予知保全のビジネスケースは何かを検討するだけでなく、企業は従業員を戦略に組み込む一緒に進める必要があります。
RSのオートメーションと制御機器については、こちらをご覧ください。