- 発行日 2024年12月3日
- 最終変更日 2024年12月4日
- 1 分
産業分野のメンテナンスにおけるデジタルトランスフォーメーション
第4次産業革命は、製造業の働き方を急速に変革しており、機械のukも例外ではありません。本ガイドでは、AI、産業用IoT(インターネット・オブ・シングス)、およびデジタルツイン技術が、機器製造業における予測分析の導入をどのように支援し、機械の故障を未然に防ぐだけでなく、生産性向上、コスト削減、さらには健康・安全面の改善に寄与しているかを解説します。
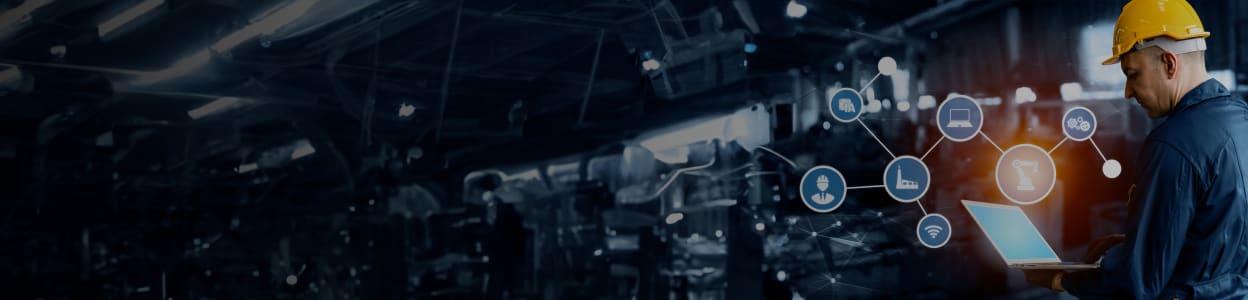
産業分野でのデジタルトランスフォーメーションが急速に進行しています。現在、産業のデジタル化は、素材や資源の調達からサプライチェーン管理、設計プロセス、製造、最終的な商品配送に至るまで、産業プロセス全体を包括しています。その中でも、保守はデジタル技術が大きな影響を与えている分野の一つであり、新技術の能力向上に伴い急速に変化しています。
実際、産業保守におけるデジタルトランスフォーメーションの枠組みは、第4次産業革命の一環と言えます。AI(人工知能)、機械学習、ビッグデータといった最新技術に加え、物理的システムがインターネットに接続される「産業用IoT(IIoT)」の普及が、製品の製造方法に大きな変革をもたらしています。産業のデジタル化が進む中で、機械の保守にもこれらの技術を取り入れることで、多くのメリットが期待できます。
デジタルメンテナンスとは?
メンテナンス分野のデジタルトランスフォーメーションでは、技術、データ、分析の進歩を活用し、より効果的な機械の維持管理を実現していますたとえば、予知保全では、機械の状態を継続的に監視し、重大な問題が発生する前に診断を行います。このアプローチでは、センサーのネットワークを活用し、設備のパフォーマンスに関する膨大な量のデジタルデータを収集・分析します。こうした方法は、機械が故障してから修理を行う事後保全と比較すると、大きな進歩と言えます。エンジニアは、平均故障間隔(MTBF)などの一般的なメンテナンスパフォーマンス指標を用いて、デジタルメンテナンス戦略の効果を評価しています。 さらに、多くの製造業者が、CMMS(コンピュータ化メンテナンス管理システム)などの製造メンテナンスソフトウェアを活用し、メンテナンス活動の計画、スケジュール化、評価を行っています。デジタルメンテナンスが普及しつつある理由は、製造産業においてメンテナンスコストを削減し、機械の稼働時間を増加させ、生産性を向上させることが可能になるためです。 こうしたデジタルアプローチは、しばしば「スマートメンテナンス」とも呼ばれます。これもまた、インダストリー4.0の広範なトレンドや、物理的なオブジェクトとインターネットの相互接続が進む中での一環です。エンジニアは、状態監視やその他のデータ収集方法を通じて機械から膨大なデータを取得・分析し、そのデータを基にメンテナンス方針を策定しています。
新しいメンテナンステクノロジー
新しいデジタルメンテナンス技術は多岐にわたります。その中でも一般的な手法は次のようなものがあります:
予知保全
予知保全は、機械の状態を継続的に監視することで、故障が発生する前に未然に防ぐことを目的とした手法です。このアプローチは、定期的なスケジュールに基づいて保守を行う予防保全とは異なりますが、どちらも事後対応型の保守ではなく、プロアクティブ(予防的)な保守として分類されます。
予知保全では、振動解析などの状態監視技術を利用して、振動の速度や周波数といったパラメータを継続的に評価します。このデータに異常が見られる場合、表面化する前の機械の問題を示している可能性があります。その場合、エンジニアは計画的な保守作業を実施して問題を解決できます。
予知保全で使用される技術は、振動監視にとどまりません。たとえば、赤外線サーモグラフィは部品から放出される熱の変化を検知し、超音波技術は音の変化を通じて漏れを検出するなど、幅広い技術が活用されています。これらの技術を組み合わせることで、より精密な状態監視と迅速な対応が可能になります。
赤外線サーモグラフィは、設備や機械の温度を非破壊で測定・監視する優れた方法です。この技術を使用することで、稼働温度を監視し、機器が最適な状態で動作していることを確認できます。また、放置すれば重大な問題に発展しかねない異常を早期に検出することが可能です。
超音波監視では、漏れ箇所、電気的な放電、または問題を示す特定の音を正確に特定できます。これは、機械設備や漏れが幅広い音を発生させるためで、高周波の短波信号は方向性が強く、特定の場所に集中する傾向があります。これらの音は背景ノイズから分離され、正確な発生源を特定することができます。超音波は特に感度の高い状態監視技術であり、微妙な音の変化を捉えることで、表面化する前に機械の問題を検出することができます。
他の技術には、オイル分析があります。これは、オイル中の金属粒子や粘度の変化が機械の摩耗を示す場合に利用されます。また、モーターに関しては、モーター状態分析があり、電動モーターの性能データを収集して故障を検出します。
これらの技術に共通するのは、いずれもデジタルデータを収集し、未来の問題を予測するために分析を行う点です。このような手法を活用することで、エンジニアは機械への損傷を未然に防ぐことが可能になります。
インダストリ4.0とメンテナンス
インダストリー3.0が、コンピューターやロボットのようなオートメーション技術を製造業に導入する時代だったとすれば、インダストリー4.0は、産業用IoT(IIoT)、ビッグデータ、人工知能を通じたデジタル化の時代です。ネットワーク化されたセンサーやデジタルデータを収集する技術を組み込むことで、機械などの製造資産をスマート化することが可能になります。これにより、機械が問題を抱えた際にその状態を知らせてくれるようになります。
この進化は産業保守に大きな影響を与えます。なぜなら、機械の故障を予測することが可能になるからです。故障を予測できれば、機械のダウンタイム(稼働停止時間)を防ぐことができ、効率性が飛躍的に向上します。
オートメーションとメンテナンス
製造業では、食品・飲料や医薬品産業をはじめとするさまざまな分野で、ロボット、コンベアベルト、数値制御工作機械(CNC)、自動プロセス技術といったオートメーションに依存しています。産業オートメーションは通常、プログラマブルロジックコントローラー(PLC)、PC、その他の制御システムといった電子機器を活用し、タスクを自動化します。PLCコントローラーは、プロセスや機械機能、さらには生産ライン全体の自動化を実現することが可能です。
オートメーションの大手であるABBによると、オートメーションの黎明期には、設備に関する情報を収集するのが困難で、保守エンジニアが現場に出向き、自動化された機器の問題を修理するのが一般的でした。しかし、デジタル技術の進化により、現在では多くの故障がリモートで診断可能となり、機械のパフォーマンスも評価できるようになりました。これにより、技術者のスキルと相まって、オートメーションを利用する製造業者が、事後保全から予防保全へと移行することが可能になりました。
AメンテンナンスにおけるAIの活用
ビッグデータはエンジニアに対してより多くの情報を提供する点で優れていますが、その情報を解釈し、行動に移せなければ意味がありません。そこで人工知能(AI)が活躍します。AIはエンジニアが機械のメンテナンスから非常に大量のデータを収集・処理し、必要なメンテナンスとそのタイミングについて予測するのを助けます。AIを用いた予知保全は、機械の信頼性を向上させ、設備の故障を回避します。また、エラーを最小限に抑えることで製造品質を向上させることもできます。しかし、AIは扱う情報に依存するため、例えば振動監視アプリケーションではデータ収集が一貫して行われる必要があります。デジタルツインによる予知保全—製造プラント全体やプロセスをシミュレーションしたり、物理資産の仮想レプリカを作成したりする技術—も、メンテナンスのためのデータ分析をより効率的にしています。
メンテンナンスにおけるデータの活用
機械からは膨大な量のデジタルデータを得ることができます。この情報は、機械のメンテナンスをより効率的に行うために利用できます。運用データは機械の健康状態に関する多くの洞察を提供し、エンジニアに対してメンテナンス活動の範囲とタイミングを示し、問題が悪化するのを防ぎ、最終的には機械の故障を防ぐ手助けをします。そのすべてのデータを迅速に手作業で分析することは不可能です。そのため、予知保全のためのデータ分析には、データを抽出し、有用な活用方法を検討するためにAIや機械学習などの関連技術が必要となることが多くなっています。
メンテンナンスにおけるIoTの活用
IoT(モノのインターネット)およびIIoT(産業用モノのインターネット)とは、インターネットに接続された様々な機器のネットワークを指します。メンテナンスにおいて、IoTはセンサーやその他の技術が収集した情報をネットワークを介して収集する仕組みを意味します。
このデータ収集および伝送機能のおかげで、予知保全のための予測分析が可能となり、メンテナンスの必要性を事前に把握することができます。
メンテナンスにおけるデジタルツイン
デジタルツインとは、物理的なオブジェクトや製造プロセスを仮想的に再現したものです。デジタルツインを作成することで、以下のような活用が可能になります:
- シミュレーションの実施
- 資産の性能分析
- 改善案の提案
提案された改善案は、物理的な対象に適用することができます。
特にメンテナンスの分野では、デジタルツインを活用することで最適なメンテナンス戦略を決定できます。デジタルツインがない場合、効率的な戦略を策定するには膨大な時間やコストがかかる可能性があります。
デジタルトランスフォーメーションの利点
デジタル保守の利点には、機械の稼働時間の増加から生産性の向上、さらには健康・安全文化の改善に至るまで、さまざまな効果があります。プロアクティブな保守はデジタル技術に依存しており、特に予知保全はこれなしでは実現できません。予知保全への投資の初期費用が高く感じられるかもしれませんが、製造業の組織は、投資収益率(ROI)が初期コストを大きく上回り、さらに安全規制の遵守、資産の寿命延長、スタッフの効率的な活用、製造能力と生産性の向上など、さまざまな利益があると報告しています。対照的に、予防保全の運用は、現在ではCMMS(コンピュータ化保守管理システム)などのデジタル技術によって支援されることが多くなっています。
要するに、第4次産業革命が進展する中で、デジタル技術は最先端の保守戦略を開発するエンジニアにとって欠かせないものとなっています。製造業者はデジタル保守を導入し、その過程で業務を変革しています。
RSが職場のオートメーションにどのように役立つかについて、さらに詳しく学んでみてください。