技術情報 > 実録ものづくりレポート > 液晶パネル搬送ロボット開発秘話
液晶パネル搬送ロボット開発秘話
紙のように薄いガラスを取り扱う巨大ロボットに知恵を集結
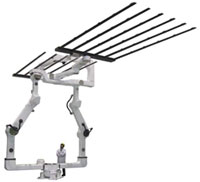
産業用ロボットで国内最大手の安川電機。自動車用の溶接塗装ロボットから、半導体シリコンウェーハや液晶ガラスを搬送するロボットなど、さまざまな産業用ロボットを手掛けている。このほど大手パネルメーカーに納入された第10世代液晶パネル向けの搬送ロボットはこれまでの方式とは全く違う。全社の英知を結集、部門の垣根を超えて生まれた新型ロボットの開発秘話を紹介する。
大型液晶ディスプレイ用の搬送ロボット技術は、これまでの産業用 ロボットにはなかった難しい課題を持っていた。それを克服して第10世代の液晶パネル搬送ロボットを2007年11月末に発表、12月から 販売を開始した。この第10世代の液晶パネル搬送ロボット「MOTO- MAN-CDL3000D」は、2008年12月に経済産業省の「今年のロボ ット大賞」2008の優秀賞8件の中の日本機械工業連合会会長賞という賞を受賞した。
この第10世代の液晶パネルは、製造するガラス基板の大きさがなんと、2.85m×3.05mという畳5畳強分の大きさで厚さが0.7mmと 超薄いガラス基板(マザーガラスとも呼ぶ)の上に作り込む。ここまで巨大なガラスが必要なのは、従来の2.16m×2.4mの第8世代のガラ ス基板では42インチ液晶テレビ画面が8枚しか取れないが、第10世代だと15枚も取れるからである。すなわち液晶テレビ用パネルの生産性がほぼ2倍になり、その分液晶パネルをコストダウンできる。
紙のように薄いガラス基板を運ぶ
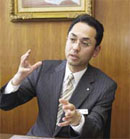
この薄くて巨大なガラスを、製造装置から製造装置へあるいは、製造装置からカセットへと搬送するのが、このロボットだ。このガラスのイ メージは、A4サイズの一般普及のコピー紙の厚さ0.1mmと比べると わかりやすい。A4サイズは210mm×297mmだから、第10世代のガ ラス基板はA4の紙よりも134倍大きく、厚さがわずかに7倍しか厚くない。A4の普通コピー紙よりもし なやかでぺらぺらという状態。いわ ば割れやすい「紙 」を運ぶような ロボットである。もはや「ガラス基 板というより流体に近い」と、同社 クリーンロボット事業統括部の大倉正彦統括部長(写真)は語る。
現実にはこの割れやすい「紙」 より薄い巨大ガラス基板をハンド リングするわけだから、それだけで も大変難しい制御技術である。し かも、液晶ガラスは熱処理装置などのプロセス装置へ出し入れする ために、上下のストロークは4~4.5mという高さに渡って出し入れする必要がある。しかも液晶製造装置は、1時間に何枚のガラスを処理で きるか、というスループットを上げなければならない。このためハンドリングロボットにも高速動作が要求される。また、4.5mという高さを行き来 するロボットが大き過ぎては液晶工場に搬入できない。トラックに積んで運べるサイズにまとめなければならない。もちろん、液晶工場はクリ ーンルーム内で作業するわけだから、発塵防止は言うまでもない。
こういった難題にチャレンジして見事克服したのが、この新型ロボットである。今、大手パネルメーカーに納入し終えたところだ。
従来技術の延長では実現困難
今回の「MOTOMAN-CDL3000D」を開発するに当たり、従来の同社の機種でも他社の機種でもロボット技術の延長では実現が難しいことがわかってきた。同社の従来の昇降直動タイプ機種では、上下運動は4~4.5m必要なため、上下の支柱を途中で切って現地で組み立てていた。このためパネルメーカーは再組み立ての日程の調整が必要だった。クリーンルームの入口は1ヵ所か2ヵ所しかなく、ロボットは奥から入れていく。このため分刻みで順番どおりに搬入していかなければ 予定のスケジュールに間に合わない。液晶パネルメーカーはこの直動型ではこれはやむを得ないと思っていた、と大倉部長はいう。しかもこの 直動タイプでは、自転車の空気入れのように、内部の空気を吸って排出するような仕組みになっているためフィルタが必要であり、定期的にフィルタを交換しなければいけなかった。基本的にメンテナンスフリーにしたい。
一方、昇降シングルリンクタイプ機種では、人間の膝のような上下軸のストロークを使う。しかし4.5m必要な場合、長くなり過ぎてしまい構造的に製造しにくい。アームを1本2m以上にしないとその上下運動範囲 を実現できない。現実的ではない。また、できるだけ小さな床面積の中 でモノづくりをしたいが、折りたたむ時にその出っ張り部分が大きくなってしまう。ただし、空気の出し入れをする機構がないためメンテナンス フリーという利点がある。
液晶、自動車用両チームの英知を絞り出す
どちらも一長一短があるため、今回のような大型ガラス基板には機構をそのまま大きくしても実現できない。それで、今回のプロジェクトには安川電機のロボットチームの英知を集めることにした。直接関係する液晶ロボット開発グループのほかに自動車用ロボットのグループも参加させて、両グループで知恵を出し合った。液晶グループはユーザーニーズを熟知しており、自動車グループは違うニーズから別のノウハウ 技術を持っている。いわゆる異業種に近く、眠っている技術の構想を引き出すという意味もあったと大倉部長は言う。
定期的な会合を開き情報の共有化を含めて、当時は1週間に1回、 知恵を出し合った。構想を練り上げるのに3ヵ月から5ヵ月かけた。結論が出た後は試作機の完成まで早かった。わずか3ヵ月で作り上げた。 「出来てしまえば、簡単なように思えるが、自分たちの思考の垣根を打ち破って、新しいものを作り出した」。
4.5mの上下運動を高さ2.5mの機械で実現
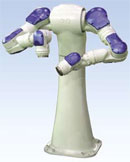
出来上がった今回の「昇降ダブルリンク式支柱タイプ」では、上下軸 が二つのアームで構成されている。アームの支点(ポスト)を二つ持ち、 第一のアームの先端に第二の支点を持つアームを設置し、二つのアー ムで上下運動をする。この構造を左右2台(一対)持っている。駆動用 のモーターは片方のアームに2個設けており、左右で4個という構成だ。この構成にすることで、剛性を上げることができた。かつ、4つのモーター を協調制御させることで上下方向だけではなく左右方向の動きにも対 応できるようにした。また、左右方向へのひねり動作も可能にした。
下側の第一の支点ではアームは180度動くことが従来とは大きく違う。従来の昇降シングルリンク方式では90度しか動かなかった。「いわゆる従来は北半球しか動けなかったが、今回は北半球から南半球 まで動けるようになった」と大倉部長は言う。この結果、アームをたたんだ時の全高が2.5m以下という低さを実現できた。
新型ロボットでは、3m基板を秒速4mの速度で水平方向に動かし、7~8m先の先端部分の揺れが上下±4mmレベルという高い精度を実現している。加えて、ガラス基板の水平方向のずれが±50mm なら補正できるという補正制御も行っている。いずれも4つのモーターの協調制御により実現した。このため従来なら水平補正用の装置が別に必要だったが、これが不要になり、設備費を削減できる。
この新型ロボットの新技 術を第7世代、第8世代の 液晶パネル工場向けにも下方展開し、広げていく。さらに液晶だけではなく、薄膜太陽電池パネル工場にも活かせるとみている。